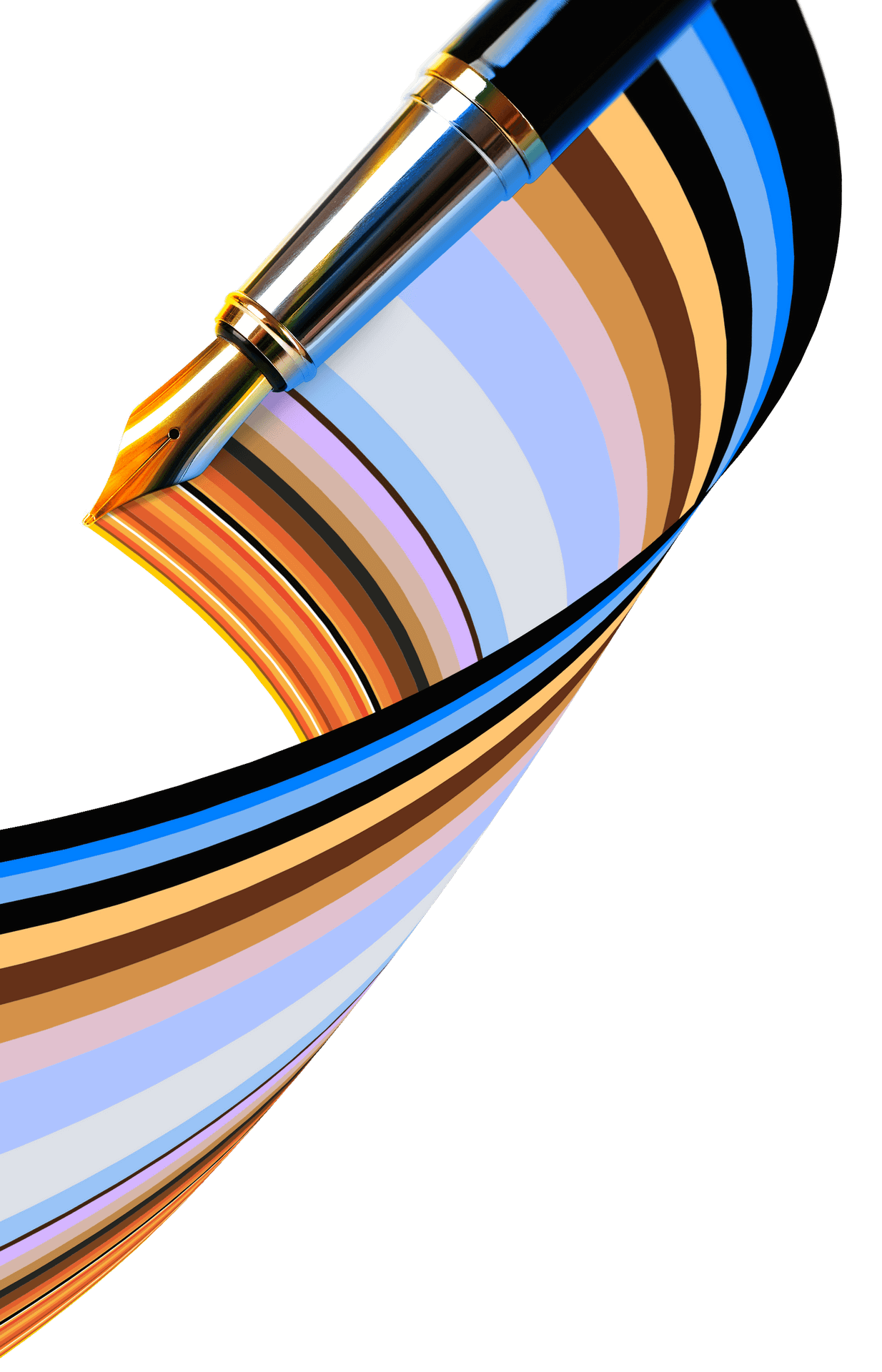
Management
58%
EBITDA margin
Nornickel considers social responsibility and commitment to the principles of sustainable development as key operational priorities for business development, community and investor relations, and environmental impact management.
Achievements
Horizons
In 2019, we joined the Hyperledger Project, a global collaboration hosted by the Linux Foundation, one of the largest and most reputable technology consortia supporting the creation of sustainable open source ecosystems.
In October 2019, Nornickel helped host Russia’s first ever Hyperledger Bootcamp, a major educational and networking event for IT professionals and startups, as well as representatives of large companies involved in IT development and support.
Programmes
Technology Breakthrough is an ongoing programme to introduce advanced digital technology in mine engineering, as well as in planning and operational control of mining activities.
Projects
In 2019, as part of its efforts to build a talent pipeline, Nornickel signed a trilateral agreement to launch a master’s programme in blockchain at the Moscow Institute of Physics and Technology (MIPT). The agreement was signed at the St Petersburg International Economic Forum.
Nornickel is at a stage where we are ready to take a big step not only towards solving the issue of SO2emissions, but also to join the global environmental agenda.
We cannot just keep on doing business as usual, even though our reserves are vast, our financial and operating performance is encouraging, and our return on invested capital is industry-leading.
The Company has finished putting together an industrial development and subsoil use strategy for the coming ten years. The strategy needs to include sustainable development requirements and parameters in the face of growing climate risks, societal expectations for greater transparency and investor demands. The idea is to show how the Company responds to these challenges and what changes it triggers in production and financial modelling.
This vigilant approach, taking into account climate risks, will undoubtedly further compliment our existing competitive strengths. We cannot disregard the potential tightening of legislative and regulatory requirements already imposed on industrial companies by the government (automatic accounting of emissions, quotas, etc.), either.
Given the circumstances, we should disclose full information on what impact the transition to a low-carbon economy will have on us and how we envisage a strategy for reducing greenhouse gas (GHG) emissions. Importantly, Nornickel currently leads the pack among M&M companies in terms of total GHG emissions.
We are considering disclosure in our sustainability report in line with the TCFD (the FSB Task Force on Climate-Related Financial Disclosures) recommendations and planning to further develop non-financial reporting in the following periods.
The management understand the need for these measures and is ready to convince Nornickel’s employees not only to comply with the existing environmental programme unconditionally, but, most importantly, to take strategic and tactical steps that can effectively reduce the environmental footprint all along our production chain. We have already established a senior team under my supervision and have given it executive powers. One of their first tasks is to develop climate change scenarios.
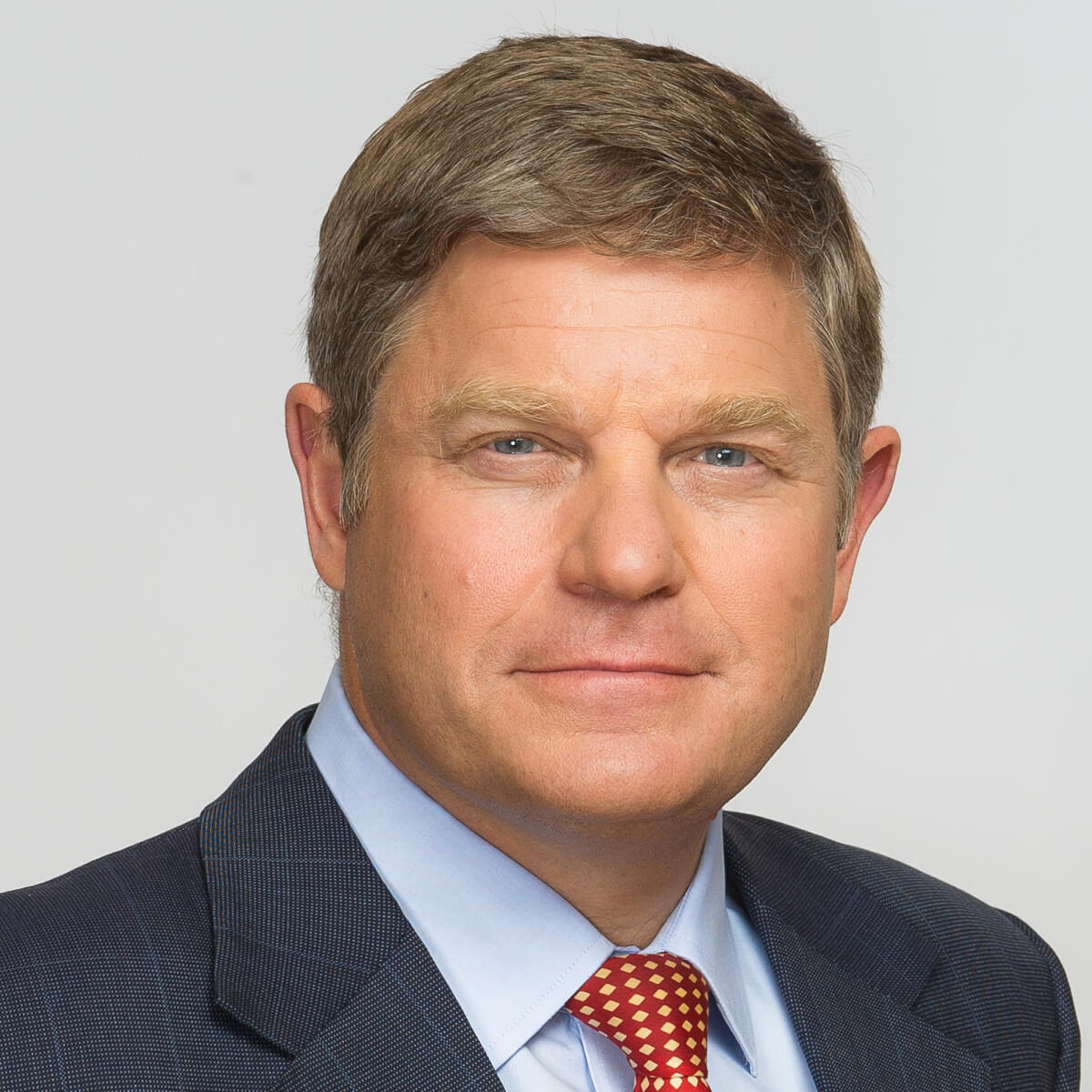
Gareth Penny
Chairman the Board of Directors
of MMC Norilsk Nickel
Sustainability management
Corporate governance
Nornickel’s corporate governance framework is designed to take into account and balance the interests of shareholders, the Board of Directors, managers, employees, and other stakeholders. 102-26
Our key approaches and principles serving as a basis for an effective governance framework draw on the applicable Russian laws, including the Corporate Governance Code recommended by the Bank of Russia.
Nornickel’s governance framework relies on the following principles:
- equitable and fair treatment of every shareholder;
- support for the shareholders to let them exercise their rights and lawful interests in the most reasonable and convenient manner;
- professionalism and leadership of the Board of Directors, and involvement of independent directors in governance;
- strategic management by the Board of Directors, its efficient control over executive bodies, and oversight of the risk management and internal control framework; sound, bona fide and efficient management of the Company’s day-to-day operations by executive bodies accountable to the Board of Directors and the General Meeting of Shareholders;
- compliance with the Russian laws and the national laws of the countries of operation;
- corporate social responsibility;
- strong business ethics;
- zero tolerance to corruption, and effective anti-corruption measures;
- full, transparent, reliable and timely disclosure;
- robust internal controls, internal and external audits;
- active collaboration with investors, creditors, and other stakeholders in order to increase the Company’s assets and market capitalisation. 102-25
These principles are reflected in Nornickel’s official documents, including the Articles of Association, Regulations on the Board of Directors, Information Policy Regulations, Anti-Corruption Policy, and other by-laws*. 102-27 102-28
Governance structure 102-18 102-20
Pursuant to MMC Norilsk Nickel’s Articles of Association, its governance bodies are:
- the General Meeting of Shareholders, the Company’s supreme governance body;
- the Board of Directors, a collegial governance body in charge of strategic management and oversight of the executive bodies;
- the Management Board and the President that represent the collegial and sole executive bodies of Nornickel, respectively, and manage day-to-day operations.
In 2019, we enabled the sign-up to the Shareholder’s Personal Account in our Registrar’s mobile app using a unified identification and authentication system. This was done as part of our efforts to make information more accessible to our shareholders.
The Board of Directors meets as and when required, but at least once every six weeks. In 2019, the Board of Directors met on a quarterly basis to review the Company’s financial results, progress against the strategy, the management’s HSE reports, and operational performance reports. In 2019, the Board of Directors of MMC Norilsk Nickel considered 129 matters, including 29 deal approvals, 76 corporate governance matters, 12 economic and financial matters, 1 social and environmental matter, and 11 other matters. 102-19 102-29 102-31 102-33 102-34
In the reporting year, the attendance rate of the Board meetings was 99.77%.
In overseeing the Company’s management, financial and business affairs, the Board of Directors may instruct the management team on individual matters and monitor implementation of resolutions and tasks. Authorised executives are vested with powers and responsibilities to address economic, environmental and social matters and may delegate their powers to other employees based on their competences and functions. 102-20 102-21
The reporting year saw an external assessment of the Board of Directors performance in 2018.
The Board of Directors has four committees.
Committees of the Board of Directors |
Directors |
Chairman |
Share of directors |
||
Independent |
Non-executive |
Independent |
Non-executive |
||
Audit and Sustainable Development Committee |
5 |
+ |
+ |
60% |
40% |
Budget Committee |
5 |
+ |
60% |
40% |
|
Strategy Committee |
5 |
+ |
+ |
80% |
20% |
Corporate Governance, Nomination and Remuneration Committee |
5 |
+ |
+ |
60% |
40% |
The President and the Management Board are the Company’s executive bodies. In the reporting period, the position of the Company’s President was held by Vladimir Potanin who concurrently chaired the Company’s Management Board. As at the end of 2019, Vladimir Potanin had held the position of the President (CEO before 2015) for 7 years and 13 days.
Operational sustainability management
The governance and executive bodies of MMC Norilsk Nickel and its subsidiaries are in charge of implementing the Company’s sustainability goals and objectives within the scope of their functions and in accordance with the applicable laws and internal regulations*.
All executive efforts are coordinated by MMC Norilsk Nickel’s Management Board, President, and a number of executive committees: the Budget Committee under the Management Board, Health, Safety and Environment Committee, Investment Committee, Nomination and Remuneration Committee, and Charity Committee.
Compliance with the key international standards in quality and HSE
Company |
Compliance of the management system with international standards |
External audits in 2019 |
Certification scope |
MMC Norilsk Nickel |
ISO 9001:2015, |
Surveillance audit |
Production, project management, storage, delivery, including by sea, and sales (nickel, copper, cobalt, precious materials, sulphur, selenium, tellurium) |
Kola MMC |
ISO 9001:2015, |
Recertification audit |
Mining and processing of ore, production of nickel, copper, cobalt, their compounds, precious metal concentrates, sulphuric acid |
Gipronickel Institute |
ISO 9001:2015 |
Surveillance audit |
R&D, design, engineering surveys, engineering and environmental activities, project management in mining, concentration and smelting, and relevant inspection methods; development of standards for non-ferrous metal industry products and their inspection methods; development of reference standards for the composition of non-ferrous metal industry products |
Norilsk Nickel Harjavalta |
ISO 9001:2015, |
Surveillance audit |
Manufacturing of nickel and cobalt products |
ISO 45001:2018 |
Certification audit |
Operational management 102-18 102-20
Nornickel’s management team is made up of professionals with extensive experience. In 2019, seven managers of Nornickel made it to Russia’s Top 1000 managers annual ranking published by the Russian Managers Association in collaboration with the Kommersant publishing house. Pavel Platov, Nornickel’s Corporate Secretary, received the Director of the Year 2019 award in the Corporate Governance Director category. Larisa Zelkova, Senior Vice President for HR, Social Policy and Public Relations, was named the winner in the individual PR Director of the Year category of the largest communications award in Eastern Europe and Central Asia — Eventiada IPRA Golden World Awards.
We have created an extensive regulatory framework of over 20 internal documents to help integrate sustainability aspects into our management practices and day-to-day operations of our functional units.
Our management systems are aligned with best international practices and standards. For many years, we have been successfully running the Corporate Integrated Quality and Environmental Management System (CIMS). In 2017 we also kicked off an efficiency improvement programme seeking, among other things, to introduce innovative management approaches.
In 2020, we will continue to develop and bring our by-laws in line with the best practices in corporate governance and business ethics.
Remuneration
Remuneration of members of the governing bodies
Key principles and mechanisms of remunerations due to the governing bodies are set out in the the by-laws of the Company.1 Nornickel’s remuneration framework is continuously and closely monitored by the Board of Directors. 102-35 102-36 102-37
The Board of Directors’ annual remuneration is set out in the Remuneration Policy for Members of the Board of Directors* approved by the General Meeting of Shareholders.
The annual remuneration for non-executive directors includes:
- base remuneration of USD 120,000 for the Board membership;
- additional remuneration of USD 50,000 for membership in a committee of the Board of Directors;
- additional remuneration of USD 150,000 for chairing a committee of the Board of Directors;
- reimbursement of expenses incurred by directors in discharge of their duties.
In 2019, the Annual General Meeting of Shareholders established remuneration for the Chairman of the Board of Directors, an independent director, in the amount of USD 1 mln per year, paid on a quarterly basis in equal instalments in roubles at the exchange rate of the Bank of Russia on the last business day of the reporting quarter*.
KPIs used by the Company to assess the senior executives’ performance reflect the achievement of Nornickel’s strategic objectives.
According to the Company’s Articles of Association, decisions on remuneration and reimbursement payable to the Company’s President and members of the Management Board are reserved to the Board of Directors. The remuneration of senior executives consists of the base salary and bonuses. Bonuses are linked to the Company’s performance, including both financial (EBITDA, free cash flow) and non-financial indicators (workplace injury rates, labour productivity). Specifically, at least 20% of collective corporate KPIs are linked to a reduction in the Group’s total number of reported injuries; in case of fatal accidents, 20–30% of the annual bonus is not paid to the heads of production units (including the COO).
Performance management
103-3
404-3
Nornickel has been operating a performance management system for six years, with assessment relying on key performance indicators (KPIs), including occupational safety, efficiency improvements and capital management. The KPIs factor in cross-functional interests of process participants. In 2019, the KPI-based assessment covered 11,300 employees.
The system helps streamline evaluation criteria, enables the management and employees to align the current year’s priorities with performance indicators of the Company/divisions/subsidiaries and link an employee’s performance to their pay level.
The performance assessment runs as an automated subsystem of the existing MIS. As at the year-end, the system covered 28 Nornickel’s divisions and subsidiaries. In 2020, it will be rolled out at the remaining facilities of the Group.
Competency management
In 2019, the corporate and management competencies model was used to assess candidates at the recruitment stage, evaluate employee performance and potential, and add them to the talent pool. The outcome of evaluating the managerial and leadership potential served as a key criteria for selecting managers with strong career growth prospects.
In 2019, we developed and integrated a 360-degree corporate and management competency review into the MIS as a module. The automated assessment exercise can be rolled out at all our sites to secure uniform approaches to personnel assessment and development.
In terms of professional competency management, the reporting year saw us define knowledge and skill requirements for the Industrial and Occupational Health and Safety function, Polar Division’s and Kola MMC’s metallurgical operations and the operating unit at Polar Transport Division. We developed a bank of test questions and evaluated the level of employees’ professional competencies.
In 2019, the Company continued to develop and train the talent pool, and high-potential executives from our facilities were trained under Nornickel’s Leaders corporate programme.
In 2020, we plan to continue rolling out the automated corporate and management competency assessment system at the Company’s sites. As part of it, we will start automating professional competency management processes, while also making those related to organising and holding HR committee meetings, and selecting high-potential managers fully automated. We will also proceed with the diagnostics and management of professional skill development across our operations. Our plans include building a professional competency model for a number of functions and operations, such as transportation, HR management, geology and surveying, concentration, repairs, gas extraction and supply. About 3,500 employees are expected to complete professional competency tests in 2020.
Competency assessment in 2019
Competencies |
Participants |
Outcome |
Assessment of potential, current performance and development prospects of middle and top managers |
Managers from a number of the Group’s key operations |
Successors for 150 managerial positions determined 109 high-potential managers trained under Nornickel’s Leaders corporate programme |
A 360-degree corporate and management competency review using the in-house model |
444 managers from the Head Office functions and a number of the Group’s key assets |
|
Assessment of professional competencies for managers and the blue-collar staff at the Head Office and mining operations |
635 managers and white-collars |
Areas for personal and professional development identified |
Employees covered by assessment in Russia, FTEs
Indicator |
Blue-collar employees |
White-collar employees |
Managers |
Group total |
Competency assessment |
||||
Male |
198 |
236 |
1,549 |
1,983 |
Female |
15 |
108 |
348 |
471 |
Total |
213 |
344 |
1,897 |
2,454 |
KPI-based assessment |
||||
Male |
27 |
2,058 |
4,208 |
6,293 |
Female |
8 |
3,331 |
1,698 |
5,037 |
Total |
35 |
5,389 |
5,906 |
11,330 |
Assessment of employees in Russia, % of average headcount
Indicator |
Blue-collar employees |
White-collar employees |
Managers |
Group total |
Competency assessment |
||||
Share of employees covered by competency assessment |
0.4% |
2.6% |
18.1% |
3.4% |
Share of male employees covered by competency assessment |
0.5% |
3.8% |
19.4% |
3.7% |
Share of female employees covered by competency assessment |
0.1% |
1.6% |
13.8% |
2.4% |
KPI-based assessment |
||||
Share of employees covered by KPI-based assessment |
0.07% |
41.05% |
56.26% |
15.6% |
Share of male employees covered by KPI-based assessment |
0.07% |
33.25% |
52.74% |
11.9% |
Share of female employees covered by KPI-based assessment |
0.08% |
48.00% |
67.43% |
25.5% |
Risk management framework
We have put in place an effective risk management framework.
Key objectives:
- increase the likelihood of achieving the Company’s goals;
- make resource allocation more efficient;
- boost the Company’s investment appeal and shareholder value.
The risk management framework is based on the principles and requirements of the Russian and international laws and professional standards, including the Corporate Governance Code recommended by the Bank of Russia, ISO 31000 (Risk Management) and COSO ERM (Enterprise Risk Management — Integrated Framework).
We have formalised our risk management structure, allocating relevant roles and duties to all employees. The Board of Directors defines the principles and approaches to organising a risk management framework and oversees its performance. 102-30
For more details on the risk (including financial risk) management framework and initiatives, please see MMC Norilsk Nickel Annual Report for 2019.
We continuously improve and develop our corporate risk management framework. The key focus areas are set forth in the relevant roadmap in line with standards, international risk management practices, maturity models of risk management processes, and recommendations of the management and Board of Directors.
Key risk management participants and their functions 102-29 102-30
Our main achievements in risk management for the last three years:
- Developing and approving a risk management package, including policies, regulations, function-level SOPs, and business continuity planning guidelines.
- Listing the Group’s key risks. The Board’s Audit and Sustainable Development Committee and the Management Board regularly review a strategic risk map and a list of Top 20 risks. Following the assessment, the boards make management decisions, including drafting and approval of risk management plans.
- Including key business units in the corporate risk management framework. Subsidiary risk reports are subject to analysis at all levels and subsequent consolidation in the Head Office on a regular basis.
- The Board of Directors’ approval of the Risk Appetite Statement to be updated annually going forward.
- Drafting and approval of business continuity plans for the most critical production and infrastructure risks.
Actions to be taken under the 2020+ risk management roadmap:
- Embark on risk management automation and fine-tuning early risk warning procedures based on a GRC approach.
- Perform regular self-diagnostics and assessment of the risk management framework for compliance with the best global practices.
- Start developing key risk indicators as part of GRC introduction.
- Roll out simulation modelling to investment risk assessment.
- Broaden the business continuity management scope to include non-production processes (IT, security, staffing).
New risk management
Traditionally, new risks arise from exposure to external threats. These risks are often hard to analyse and prevent due to the lack of information. Effective control over newly identified risks is important for securing our stability in the long run, managing changes and maintaining our competitiveness in metals markets. We assess and manage new risks with due regard to their potential effects, the speed of materialisation and our actual ability to prevent and/or mitigate such risk events.
New risks are identified and monitored, at the initial stage, by in-house professionals, including risk experts that pre-identify and evaluate risks in all areas of our business. Risk owners start acting on new risks following the assessment of the Company’s exposure and the necessary response measures.
When dealing with new risks, we focus mainly on their prevention and mitigation. The steps we take include introducing relevant controls, such as business continuity plans for external risks that may negatively affect our production operations and business processes. These controls help strengthen Nornickel’s resilience to critical situations that occur in the external environment. New risks are subject to regular assessment, including the review and analysis of their materiality for the Company.
Insurance
Insurance is one of the key tools for managing risks and finances and protecting the assets of the Company and its shareholders against any unforeseen losses related to its operations, including due to external hazards.
The Group has centralised its insurance function to consistently implement uniform policies and standards supporting a holistic approach to managing insurance policies and fully covering every risk at all times. Every year, we approve ensure an comprehensive insurance programme that defines key parameters by insurance type and key project.
Nornickel runs a corporate insurance programme that covers assets, equipment failures and business interruptions across the Group. Our corporate insurance policies are issued by major Russian insurers in cooperation with an international broker. This helps us make sure that our risks are underwritten by highly reputable international re-insurers.
The same principles of centralisation apply to our freight, construction and installation, aircraft and ship insurance arrangements. The Group companies, as well as its directors and officers, carry business and third-party liability insurance.
To secure optimum insurance terms, we follow the best mining industry practices in this domain.
Map of key sustainability risks
The map of key sustainability risks defines the most significant risks in terms of their sources and their effect on the likelihood of achieving strategic goals. Drafted in accordance with international risk management standards, this document reflects changes in risk materiality in the reporting year.
Climate risks
Climate change and global warming may impact our operations in the long run. This impact may manifest in the form of weather anomalies or irreversible changes of climatic conditions. 201-2
Physical effects of climate change (physical climate risks) that may affect our operations include soil thawing and drought. As part of our management strategy, we take a series of steps to monitor and control these risks. We also take into account climate transition risk, including market-related, toughening of environmental regulations and compliance risks.
With high consumption of electricity from renewable sources, large percentage of reused and recycled water and one of the industry’s lowest CO2 emission metrics, we are well positioned to keep this risk at an acceptable level.
Apart from threats, materialised climate risks may ultimately bring us new opportunities due to strong demand for metals needed to build a low-carbon economy.
The Board’s Audit and Sustainable Development Committee regularly analyses risk data, including information on climate change risks published in the Norilsk Nickel Group’s quarterly risk reports.
Key sustainability risks
This section presents key non-financial risks linked to our sustainability priorities, which are safety, security, environmental protection and social responsibility. For more details on other risks, please see our Annual Report for 2019. 102-15
Risk |
Description |
Mitigants |
||||||
1. Risk of toughened environmental requirements |
Toughening of environmental requirements, including procedures to obtain environmental permits and closer government oversight of compliance in this area. Key risk factors:
The Company’s strategic priorities and/or goals affected by the risk:
Risk assessment
|
To manage this risk, the Company:
|
||||||
2. Workplace injury risk |
Failure to comply with the Group’s health and safety rules may result in threats to the employee health and life, temporary suspension of operations and property damage. Key risk factors:
The Company’s strategic priorities and/or goals affected by the risk:
Risk assessment
|
Pursuant to the Occupational Health and Safety Policy approved by the Company’s Board of Directors, the Company:
|
||||||
3. Information security risks |
Potential cyber crimes may result in an unauthorised transfer, modification or destruction of information assets, disruption or lower efficiency of IT services, business, technological and production processes of the Company. Key risk factors:
The Company’s strategic priorities and/or goals affected by the risk:
Risk assessment
|
To manage this risk, the Company undertakes to:
|
||||||
4. Power blackouts at production and social facilities in the Norilsk Industrial District (NID) |
A failure of key equipment at the generating facilities and transmission networks may result in power, heat and water shortage at key production facilities of the Company’s Polar Division and social facilities in the NID. Key risk factors:
The Company’s strategic priorities and/or goals affected by the risk:
Risk assessment
|
To manage this risk, the Company:
|
||||||
5. Compliance risk |
The risk of legal liability and/or legal sanctions, significant financial losses, suspension of production, revocation or suspension of licences, loss of reputation, or other adverse effects arising from the Company’s non-compliance with the applicable regulations, instructions, rules, standards or codes of conduct. Key risk factors:
The Company’s strategic priorities and/or goals affected by the risk:
Risk assessment
|
To manage this risk, the Company:
|
||||||
6. Social risk |
Escalating tensions among the workforce due to the deterioration of social and economic conditions in the Company’s regions of operation. Key risk factors:
The Company’s strategic priorities and/or goals affected by the risk: Social responsibility:
Risk assessment
|
To manage this risk, the Company:
|
||||||
7. Risk of insufficient water resources |
Water shortages in storage reservoirs of the Company’s hydropower facilities may result in failure to achieve necessary water pressure at HPP turbines leading to limited power production and drinking water shortages in Norilsk. Key risk factors:
The Company’s strategic priorities and/or goals affected by the risk:
Risk assessment
|
To manage this risk, the Company:
|
||||||
8. Soil thawing |
Loss of pile foundation bearing capacity, deformation of buildings and structures leading to their destruction. Key risk factors:
The Company’s strategic priorities and/or goals affected by the risk:
Risk assessment
|
To manage this risk, the Company:
|
Corporate security
Nornickel is a global metals and mining leader and a strategically important company in most regions where it operates. This makes corporate security a priority area for the Group’s operations.
The corporate security system is managed based on a number of programmes to maintain economic, corporate, information, facility and transportation security along with transparency in procurement and contractor selection. We pay special attention to supporting socially significant investment and environmental projects.
Development and implementation of group-wide security measures fall under the remit of the Corporate Security Unit, acting in line with the Russian laws, applicable international regulations, internal standards and guidelines.
We take part in major international forums dedicated to information security issues, where we initiated a project to establish regional contact groups for cyber security in 2019.
In July 2019, the United Nations’ Economic and Social Council (ECOSOC) approved a resolution on combating international organised crime and its links to illicit trafficking in precious metals. To a considerable degree, it factors in Nornickel’s practical experience, including unique R&D solutions of the Company’s Office for Chemical Forensic Analysis designed to identify products containing PGM metals.
In Russia, Nornickel is actively engaged in public-private partnerships to maintain high security levels and enhance social stability at its facilities and in the regions of operation.
Our representatives are involved in developing proposals to harmonise the security laws. As at the end of the reporting year, we administered more than 30 drafts regulations on transport security, combating terrorism and other security aspects.
Also, the Company is expanding cooperation with law enforcement and supervisory authorities. Nornickel representatives participate in public and advisory boards of the Ministry of Internal Affairs, Investigative Committee, Transport Prosecutor’s Office and the Federal Security Service, and in interagency working groups. In 2019, we carried out 57 joint drills, 178 training exercises, as well as four dedicated tactical drills together with the Federal Security Service, Ministry of Internal Affairs, EMERCOM, and the Ministry of Defence.
We also piloted a system of analytical situation centres. To develop the system, the Company studied international and domestic best practices, in particular, the Secure City system.
In addition, we established a comprehensive security framework at the Bobrovy Log Fun Park (Krasnoyarsk). Following the Winter Universiade 2019 in Krasnoyarsk, a number of employees of Nonickel’s Corporate Security Unit were awarded certificates of honour for their contribution to the security of sports and cultural events.
The information security system of Nornickel’s Murmansk Transport Division was certified for compliance with ISO/IEC 27001:2013 international standard requirements, yet another milestone in 2019 for us. Successful certification confirms Nornickel’s strong information security practices, high adaptability and efficiency of measures taken to boost the resilience of its corporate infrastructure and production processes to cyber threats.
Nornickel’s special Corporate Security Department at Moscow State Institute of International Relations (MGIMO) worked actively: in the new academic year, the department introduced a number of new special teaching courses, including International Legislation and Law Enforcement Practice in Public-Private Partnerships, based on the experience of Nornickel Group and other Russian corporations and relevant case studies. The department also prepared the first Russian textbook in this field called “Corporate Security Fundamentals”.
Economic efficiency
Economic efficiency is essential for us to meet our strategic goals and deliver on our commitments to shareholders, employees, local communities and other stakeholders. 103-3
The key factors driving the improvement of Nornickel’s economic performance are investment and profitability management, initiatives on increasing the shareholder value, and best-in-industry shareholder returns.
In 2019, our consolidated revenue grew by 16% y-o-y to USD 13.6 bn thanks to increased output of all the key metals and higher palladium and nickel prices.
EBITDA climbed 27% y-o-y to USD 7.9 bn on the back of higher revenue and strict operating expenses control, while EBITDA margin totalled 58%. There was downward pressure on EBITDA stemming from USD 190 mln of provisions towards the shutdown of metallurgical facilities on the Kola Peninsula. EBITDA of Bystrinsky GOK, which was fully launched in September 2019, amounted to USD 349 mln.
In 2019, our CAPEX decreased by 15% to USD 1.3 bn due to the completion of a number of large investment projects in 2018.
Net debt to EBITDA went down to 0.9 times as at the end of 2019.
Our stable financial position is confirmed by investment grade ratings from Moody’s, S&P Global and Fitch.
In February 2019, Moody’s upgraded Nornickel’s credit rating to Ваа2, outlook stable, following an increase in Russia’s country ceilings for foreign currency debt to the same Baa2 level and an upgrade in Russia’s sovereign credit rating to Baa3 (investment grade), outlook stable.
Also, Nornickel received the highest creditworthiness rating according to the Russian national scale (ruAAA, outlook stable) from the RAEX (Expert RA) rating agency.
As at the year-end, we had credit ratings from the three leading international rating agencies and the Russian RAEX:
- Fitch Ratings: BBB– / Stable
- Standard & Poor’s: BBB– / Stable
- Moody’s: Baa2 / Stable
- Expert RA: ruААА/Stable.
In 2019, budgets of various levels saw the Group companies pay RUB 47.73 mln in fines under 412
imposed sanctions, including 21 for environmental impact, 26 for breach of labour laws, and 365
imposed on other grounds.
307-1 419-1 103-2
Financial highlights
Indicator |
2015 |
2016 |
2017 |
2018 |
2019 |
Revenue, RUB bn |
506.1 |
548.6 |
536.8 |
728.9 |
877.8 |
EBITDA, RUB bn |
277.0 |
270.8 |
270.2 |
408.2 |
542.1 |
EBITDA margin, % |
247.3 |
257.3 |
236.4 |
389.2 |
513.7 |
Net profit, RUB bn |
50 |
47 |
44 |
53 |
58 |
Assets, RUB bn |
104.0 |
167.4 |
127.4 |
187.8 |
387.6 |
Total CAPEX*, RUB bn |
974.5 |
998.3 |
958.3 |
1,059.5 |
1,205.5 |
Direct economic value generated and distributed* |
103.3 |
113.6 |
116.7 |
99.2 |
85.3 |
Direct economic value generated and distributed* 201-1
Indicator, RUB bn |
2015 |
2016 |
2017 |
2018 |
2019 |
1. Direct economic value generated |
521.2 |
554.9 |
541.0 |
734.6 |
884.6 |
2. Economic value distributed, |
554.2 |
512.7 |
519.0 |
684.6 |
918.4 |
|
175.7 |
194.6 |
194.1 |
228.5 |
239.1 |
|
7.0 |
7.4 |
17.7 |
12.9 |
14.4 |
|
104.5 |
114.2 |
120.4 |
128.8 |
136.8 |
|
222.0 |
133.4 |
128.6 |
243.1 |
383.7 |
|
45.0 |
63.1 |
58.3 |
71.3 |
144.4 |
3. Economic value retained (1–2) |
-32.9 |
42.2 |
22.0 |
50.0 |
-33.8 |
Indicator |
Number of non-financial sanctions |
Number of fines paid |
Amount of fines, RUB '000 |
Total fines and non-financial sanctions |
414 |
412 |
47,732.6 |
Environmental laws and regulations |
41 |
21 |
1,890.0 |
Anti-competitive behaviour and breach of antitrust laws |
1 |
1 |
50.0 |
Non-compliance with labour laws |
15 |
26 |
585.0 |
Non-compliance with health and safety laws |
22 |
43 |
3,567.9 |
Non-compliance with consumer protection laws, including with respect to product information and labelling |
1 |
14 |
320.0 |
Non-compliance with marketing (advertising) regulations |
1 |
0 |
0.0 |
Non-compliance with regulations on the impact of products and services on health and safety |
3 |
3 |
90.0 |
Failure to timely comply with the improvement notices issued by regulatory authorities |
44 |
52 |
12,120.0 |
Non-compliance with fire safety requirements |
15 |
2 |
380.0 |
Breach of sanitary and epidemiological laws unrelated to product requirements |
20 |
25 |
326.0 |
Breach of capital construction laws |
52 |
48 |
8,751.0 |
Breach of industrial safety laws |
131 |
52 |
13,910.0 |
Breach of transportation security laws |
12 |
17 |
780.4 |
Other grounds |
56 |
108 |
4,962.2 |
Dividend policy
Our Dividend Policy aims to balance the interests of MMC Norilsk Nickel and its shareholders, enhance the Company’s investment case and market capitalisation, and ensure respect of shareholder rights.
The Company put in place the Regulations on the Dividend Policy approved by its Board of Directors to ensure transparency on how dividends are calculated and paid out.
When calculating dividends, we account for the cyclical nature of the metals market and for the need to maintain a high level of creditworthiness. As a result, the amount of dividends may change depending on the Company’s operating profit and leverage.
Dividends paid, RUB bn
Stakeholder engagement
Stakeholders and interaction mechanisms
Effective engagement with a wide range of stakeholders is a strong contributor to Nornickel’s strategy. 102-21 102-40 102-42 102-43
As part of our operations, we seek to align and balance the interests of all stakeholders and make sure that we fully and timely disclose any material information and respond to any queries.
Our key stakeholders are employees, shareholders, investors, business partners, national and local government authorities, local communities, Russian and international non-profit organisations. We identify stakeholders based on the extent to which they interact, share interests and communicate with the Company.
At the centre of MMC Norilsk Nickel’s interaction with various groups of stakeholders is the Company’s evolving practice of ongoing dialogue in line with the international stakeholder engagement standards and accountability principles*, as well as the GRI guidelines.
Stakeholder engagement principles and procedures are set out in MMC Norilsk Nickel’s Business Ethics Code*.
The Transparency Policy of MMC Norilsk Nickel aims to provide stakeholders with complete and accurate information about our activities and ensure proper feedback.
Stakeholder map*
Stakeholders |
Key interests of stakeholders |
Interaction mechanisms |
Key interaction events in 2019 |
|
Personnel |
||||
Company employees |
|
|
|
|
Shareholders and investors |
||||
Shareholders Bond investors Investment banks (brokers) Credit, rating and ESG agencies |
|
|
|
|
Business partners |
||||
Suppliers and contractors |
|
|
|
|
The Company’s customers |
|
|
|
|
Federal authorities |
||||
Russian Federation Council Russian State Duma Russian Government Federal ministries, agencies and services Russian Trilateral Commission on the Regulation of Social and Labour Relations |
|
|
|
|
Regional government authorities and local communities |
||||
Regional government authorities Local authorities Territorial offices of federal government agencies State-run educational institutions in the Company’s regions of operation Local communities and civil society organisations in the Company’s regions of operation |
|
|
|
|
Russian and international non-profit organisations |
||||
Business associations Industry unions Non-profit organisation Russian and international sports organisations |
|
|
|
Dialogue with shareholders and investors
The authorised capital of MMC Norilsk Nickel is made up of 158,245,476 ordinary shares with an aggregate market value of USD 48.3 bn as at 31 December 2019, representing a 62.6% increase year-on-year. The Company’s ordinary shares are traded on the Moscow Exchange (ticker symbol: GMKN), while ADRs are traded in the electronic trading system of OTC markets of the London Stock Exchange (ticker symbol: MNOD), on the US OTC market (ticker symbol: NILSY) and other stock exchanges. 102-5 102-10
2019 saw a number of changes in the shareholding structure. En+ Group Plc (later renamed into EN+ GROUP International public joint-stock company — EN+ GROUP IPJSC) acquired a controlling stake in UC Rusal Plc, which, either directly or indirectly, holds 27.8% in the Company’s authorised capital. As a result, holdings of the major shareholders as at the end of 2019 were as follows: 34.6% was held by Olderfrey Holdings Ltd and 27.8% by EN+ GROUP IPJSC, while shares and ADRs in free float held by institutional and private investors from Russia, the USA, Europe, Asia, and elsewhere represented 37.6% of the capital.
In 2019, Nornickel continued its efforts to diversify the shareholder base and attract new shareholders, organising around 300 meetings with institutional investors, Investor Day in London, and conference calls to present IFRS financial statements, followed by road shows in the USA and Europe.
Responsible investment
As more and more investors and asset managers makes choices and decisions based on responsible investment principles linked to environmental, social and governance (ESG) factors, we held around 25 meetings with ESG investors in 2019. In order to improve relations with responsible investors, analysts and agencies that evaluate companies using ESG criteria, we created a separate section on the corporate website, ESG Strategy*, with all pertinent information:
Our key ESG ratings in 2019:
- ISS improved the Company’s Environmental and Social ratings to 2 and affirmed the Corporate Governance rating at 4 (1 and 10 standing for low and high risk, respectively);
- inclusion of Nornickel’s shares in the FTSE4Good Emerging Index confirmed, with a score of 3.0 out of 5;
- ESG score by the Robeco SAM investment company improved to 37 (vs 27 in 2018);
- MSCI ESG rating affirmed at B;
- Sustainalytics: the Company remains rated an Average Performer, with the total score reduced to 67 (vs 69 in 2018).
ESG assessment: the largest ratings and initiatives
Dialogue with employees
As a way to improve awareness, shape a better understanding of the Company’s goals and values, and enhance the level of trust between the team and the management, we are running a number of initiatives to establish a dialogue between senior executives and the personnel. The following activities were held as part of the project in 2019:
- 30 corporate dialogues
- 35 communication training sessions covering more than 400 managers
- 270 informal meetings
- Norilsk Live, a Q&A session with the Company’s Vice Presidents
- 6 video interviews with Vice Presidents
A total of 5,500 Nornickel employees participated in the initiative.
For more details, please see the Labour Relations section.
Dialogue with authorities and non-profit organisations
Stringent compliance with Russian laws and regional and municipal regulations, respect for mutual interests, and social responsibility are at the heart of our relations with federal and local government authorities and non-profit organisations.
Following the information transparency principle, we have initiated an open dialogue with local authorities to build constructive and effective cooperation. The Company is represented in 23 committees, commissions, expert and working groups established by governmental bodies in association with the business community, thus supporting socially important projects. Our representatives take part in parliamentary sessions and round table discussions organised by the Federation Council and State Duma of the Federal Assembly of the Russian Federation, Government of the Russian Federation, Russian Union of Industrialists and Entrepreneurs, Chamber of Commerce and Industry of the Russian Federation, Association of Managers, etc.
We take an active part in conferences, forums and business events involving policymakers and government officials, drafting hands-on proposals to optimise and develop the legal framework.
Our top management regularly attends regional authorities’ public meetings to report on the results and plans of Nornickel. In December 2019, Dmitry Pristanskov, State Secretary — Vice President and Head of GR, spoke in front of the Legislative Assembly of the Krasnoyarsk Territory to present preliminary results of MMC Norilsk Nickel’s performance for nine months of 2019 and plans going forward.
Over the past year, we backed a number of large international and domestic conferences and forums:
- Research and Practice Conference “Transport Safety Formula. Law. Knowledge. Practice”;
- 2nd Industry Conference “Water Transportation Safety”;
- International Forum “Security and Safety Technologies”;
- Conference “Fourth Industrial Revolution. Industry and Environment” (Norway);
- Krasnoyarsk Economic Forum;
- International Forum on Information Security in Garmisch-Partenkirchen (Germany);
- Forum of the Central American Parliament on International Information Security and Cybercrime (Guatemala);
- International Forum for the Peaceful Use of Information and Communication Technologies (Havana, Cuba).
Cooperation agreements
In 2019, we signed a number of agreements with federal, regional and local authorities as well as major Russian companies.
The agreements covered a wide range of social and economic issues, including infrastructure projects.
Key agreements
Partners |
Subject of agreement |
Ministry of Natural Resources and Environment of Russia Federal Service for Supervision of Natural Resources, Government of the Krasnoyarsk Territory |
|
Ministry of Industry and Trade of Russia and the Government of the Krasnoyarsk Territory |
|
Government of the Murmansk Region |
|
Administration of the Tula Region |
|
Federal Agency for Fishery |
|
Federal State Unitary Enterprise Atomflot |
|
Relocation programme
Since 2011, together with federal and regional government authorities we have been contributing to a long-term targeted federal programme to relocate people living in Norilsk and Dudinka to other Russian regions with favourable climate conditions.
The programme provides financing to help families eligible for relocation under government-sponsored programmes and registered in Norilsk and Dudinka to purchase apartments. The programme runs from 2011 to 2020. Nornickel participates in the programme as a benefactor, with its donation totalling RUB 7.8 bn as at the end of 2019. During 2011–2019, more than 7,500 families purchased apartments on the “mainland” and moved there.
Public–private cooperation on corporate security
We traditionally liaise with government agencies, including law enforcement and supervisory agencies, to ensure corporate security and safety. 103-2
Our representatives participate in public and advisory boards of the Ministry of Internal Affairs, Investigative Committee, Transport Prosecutor’s Office, the Federal Security Service, and in interagency working groups.
As a member of the International Information Security Research Consortium (IISRC), Nornickel can participate in crafting of the global information security agenda.
During the year, our representatives took part in international forums and conferences supported by Russia’s Ministry of Foreign Affairs and Security Council. Held in Norway, Guatemala, Cuba and Singapore, the events focused on the information security of business and social facilities that are critical for national economies.
In 2019, we made an emphasis on ongoing cooperation with:
- the Federal Security Service of Russia on anti-terrorism and anti-sabotage security of the Group’s critical infrastructure (fuel and energy utilities, transport infrastructure, etc.);
- the Ministry of Internal Affairs of Russia to prevent stealing of products and materials containing precious and non-ferrous metals, maintain security at public events and promote addiction prevention and awareness raising measures;
- the Federal Customs Service of Russia to prevent cross-border smuggling of metal-bearing materials;
- the Russian Ministry for Civil Defence, Emergencies and Elimination of Consequences of Natural Disasters (EMERCOM) to drill emergency responses and coordination in disaster relief operations;
- the Russian Ministry of Foreign Affairs to foster international information security and combat international crime in illegal mining, smuggling and trafficking of precious and non-ferrous metals. As part of the 28th session of the UN Commission on Crime Prevention and Criminal Justice held in Vienna in May 2019, Nornickel presented its report titled “Technology Solutions to Prevent and Combat Illegal Trafficking of Precious Metals”.
In 2019, we continued to strengthen our cooperation with the Security Council of the Russian Federation by contributing to the work of the National Association of International Information Security (NAIIS). The Club of Information Security in Industry (part of MMC Norilsk Nickel) is one of the Association’s founding organisations, with both Nornickel and the Russian Security Council represented in the NAIIS governing bodies.
The Company forms a key link in creating a global mechanism to ensure reliability of precious metals supplies. In this area, we successfully collaborate with the International Platinum Group Metals Association (IPA), where the Company acts as the Chair of the Security Committee since 2013, and with the United Nations Interregional Crime and Justice Research Institute (UNICRI). Among other projects, we are involved the SIRIO project of UNICRI, designed to develop recommendations on improving government and industry control over mining and trafficking of raw materials containing precious metals to ensure security of supply chains in a variety of industries taking into account key changes in technologies.
Environmental dialogue
Measures for reducing MMC Norilsk Nickel’s environmental footprint can be always found on the agenda of the Company and stakeholders. In the course of the year, both internal and public events feature environmental discussions. 103-2
In 2019, the following items were on the agenda of various forums and platforms:
- sustainable development of regions;
- preservation of ecosystems across the footprint of production sites;
- industrial ecology problems.
- improvement of environmental laws and regulations;
- promotion of best practices in environmental protection;
- environmental programmes and initiatives of Nornickel.
As part of the annual Investor Day held in November 2019 in London, our management updated the investment community about Nornickel’s operating and financial performance, metals market forecast, and strategic priorities, including plans to support global shift to clean mobility and a comprehensive environmental programme. For more details, please see the Development Strategy section.
Ecology was also at the top of the agenda at multiple international and domestic forums backed by Nornickel and attended by government representatives, captains of industry, investors, experts, and analysts:
- St Petersburg International Economic Forum;
- International Forum “The Arctic: Territory of Dialogue”;
- Global Manufacturing and Industrialisation Summit (GMIS–2019) (UN);
- 21st International Environmental Congress “Atmosphere 2019”;
- 2nd International R&D Conference “Problems of Maintaining Health and Ensuring Sanitary and Epidemiological Well-Being in the Arctic”;
- Conference “Best Available Techniques in Russia: Achievements and New Challenges”;
- International Conference “Technological and Organisational Innovations in Comprehensive Waste Management”;
- International Conference on Managing Mining Waste;
- 8th Ecological Forum «Corporate Responsibility to the Future. Technology for Society and Nature»;
- Russian Water Congress;
- Cross-Industry Conference “Role of Water in Industry”;
- Environmental Forum “National Environment Project: State Priorities, Business Opportunities”.
MMC Norilsk Nickel maintains active dialogue with various levels of the government and the professional community on matters of application and improvement of the regulatory framework governing environmental protection. In 2019, the key venues for discussion were:
- parliamentary hearings on the implementation of Federal Law No. 219-FZ of 21 July 2014 On Amendments to the Federal Law on Environmental Protection and Certain Legislative Acts of the Russian Federation;
- meeting in the Ministry of Natural Resources “Problems of Issuing Comprehensive Environmental Permits”;
- meetings of the Russian Government’s working group on implementing the regulatory guillotine mechanism in environmental protection and use of natural resources;
- meetings of the working group of the RSPP’s Committee on Natural Resources Management and Environment focusing on the use of fishery regulations to limit industrial impact on water bodies;
- 3rd Climate Forum of Cities held by the Government of Moscow;
- round table discussion and seminar of the Delovaya Rossiya All-Russian Public Organisation titled “Strategy of Reduced Greenhouse Gas Emissions. Global Experience and Potential in Russia”;
- open discussion of the Climate Partnership of Russia titled “Carbon Tax in Russia: Reality and Prospects”;
- workshop by KPMG titled “Climate Change: Risks and Opportunities Related to Low-Carbon Model Initiatives”;
- annual corporate workshop «Environmental Legislation: Problems and Implementation Practices».
Our representatives are closely involved in developing key draft laws on natural resources management, environmental protection, environmental impact fees, environmental charges, and amendments to laws on preferential conditions for investments in the Arctic.
Throughout 2019, our employees were active participants of working groups on improving informational and technical reference books on the best available techniques. In line with changes in environmental protection laws, we started preparations to obtain a comprehensive environmental permit for Polar Division and two sites of Kola MMC. The first stage was an ad-hoc review of sources of negative environmental impact and development of internal technological limits on pollutant emissions and discharges.
In May 2019, the visitor centre of the Pasvik Nature Reserve hosted a meeting on bilateral Russian-Norwegian cooperation in the area of environmental protection, attended by members of the Norwegian Parliament and representatives of Kola MMC. During the meeting, the participants learned more about projects implemented as part of the Kolarctic Cross-Border Cooperation Programme and included in the Working Programme of the Russian-Norwegian Cross-Border Cooperation. The participants also noted that initiatives implemented by Kola MMC had helped reduce air emissions in the Pechengsky District by more than 40% over the past five years.
Over the years, we have successfully used volunteer movements to promote dialogue on environmental protection with our employees and local communities.
One of the largest and most important annual projects of the programme is the Let’s Do It! environmental marathon. In 2019, the marathon celebrated its fourth anniversary. Some of the most exciting events of Let’s Do It! included:
- large-scale environmental festival comprising a give-away shop, lecture club, and a venue to exchange plastic for environmentally friendly products;
- urban improvement of a number of city spaces, including through the use of recycled materials;
- new workshop on plastic recycling, where anyone can make use of a shredding machine and a furnace to craft something useful out of bottles and caps they have collected.
Also, the 2019 environmental marathon saw a variety of environmental awareness raising events, clean-up days, and other volunteer initiatives.
In June 2019, we held an environmental campaign to mark the World Environment Day as a way to reduce our environmental footprint. The smelting capacities of Nadezhda Metallurgical Plant and Copper Plant were suspended for one hour. In keeping with the tradition, metallurgical operations of Kola MMC also supported the campaign as the smelting and conversion section (one reverberatory furnace, two converters and one anode furnace) of the Metallurgical Shop in Monchegorsk was idled for one hour during the day shift, along with three ore-thermal furnaces and two converters of the smelting shop in the town of Nickel.
In November 2019, Kola MMC took part in the Zero Negative Environmental Impact campaign, supported by the Bellona environmental organisation and the Government of the Murmansk Region. On 29 November, ore-thermal furnace No. 3 of the smelting shop in the town of Nickel was suspended for eight hours. The temporary shutdown was used for necessary repairs with no negative impact on the production plan.
Dialogue on public non-financial reporting
Each year starting from 2003, the Company has been engaging in dialogues with stakeholders while drafting sustainability reports.
In 2019, Moscow-based Blagosfera community centre hosted a presentation of Norilsk Nickel Group’s 2019 Sustainability Report.
For the first time ever, the Report was presented in a digital format: senior managers made a presentation live-streamed on the corporate YouTube channel. The presentation included discussions of important matters related to the Company’s efforts in sustainable development, social responsibility, environmental impact management, and community and investor relations.
The live stream, which involved international and Russian scientists and experts on sustainability, was joined by residents from across the Company’s regions of operation to ask their questions about Nornickel’s major projects. The event was also attended by members of the business community, NGOs, universities, government agencies, and the media.
Since 2014, these dialogues have also been staged as part of the We Are the City! social technologies forum. While preparing the 2019 Sustainability Report, we engaged in dialogues with stakeholders in Zapolyarny and Norilsk. Involved in those activities were employees of Nornickel in regions of operations, local authorities, businesses, NGOs, and experts on sustainable development. These dialogues helped identify the Sustainable Development Goals most relevant for the Company and the regions where it operates.
The dialogues were held in the new format of a quiz session, with participants watching the effects of digital transformation in the context of municipalities of the North. The event discussed case studies focused on the SDGs that are most relevant for the Company’s operations in the digitalisation area, and also helped provide advice on how to deliver further progress.
Number of dialogue participants as part of the 2019Sustainability Report campaign, ppl*
Supply chain management
Supply chain is a set of interrelated resources and processes leveraged by Nornickel to create value all the way from obtaining goods, materials and services to delivering end products to the consumers. Supply chain management at Nornickel seeks to ensure continuous operation of the Group’s companies, high product quality and reliability of shipments to customers. 102-9
We continuously improve the efficiency of our supply chain by adopting international best practices and standards and through business process optimisation and automation.
Key elements of Nornickel’s supply chain
Supply
Given our diverse businesses and geography of operations, the supply management function is designed to fully cater to the Company’s resource needs in a timely and efficient manner securing seamless operation of all production units and negotiating the best available procurement terms.
The importance of Nornickel’s supply function is dictated by the impact it has on:
- achievement of the Company’s strategic goals. Supply management plays a crucial role in the programme to enhance efficiency and cut costs;
- occupational health and safety. The quality of sourced products and timely supplies have a material impact on occupational health and are directly linked to the workplace safety;
- environment. An environmental impact is exerted throughout the life cycle of sourced products (production, transportation, storage, use and disposal) and is directly linked to demand planning, inventory management and logistics;103-2
- financial performance of the Group companies across the footprint. As we are the only or key customer for many local businesses, partnership with Nornickel gives suppliers an opportunity to ensure seamless operation of their enterprises and provides incentives for further growth;
- our contribution to the professional growth and cultural development of employees.
To meet the Company’s strategic environmental goals, our procurement team together with experts from other departments are looking into alternative technologies (alternative fuel and energy sources) that can reduce the Company’s environmental impact and cut costs.
The current tender procedure, in particular, includes a criterion of the supplier’s readiness to participate in the Company’s alternative energy initiatives. As part of a pilot project to build compressed natural gas infrastructure in the Norilsk Industrial District (NID), we signed business agreements to purchase special vehicles that run on eco-friendly fuels (liquefied natural gas) for production sites across the NID.
This pilot project is an example of procurement experts working in cross-functional teams that implement Nornickel’s programmes and investment projects aiming to move the NID special vehicle fleet over to fuel gas.
Being a part of our cross-functional groups facilitates the professional growth and cultural development of employees. This helps them pick up teamwork skills and learn to find solutions together. Information exchange within the remit of each of the Company’s business units offers different perspectives on problems, with all the opinions and interests factored in to provide a solid basis for reliable decisions.
Other venues for professional skill development are trade fairs and conferences, while Nornickel’s training programmes aim to broaden employees’ knowledge relevant to their jobs in procurement (in 2019, our specialists attended the Corporate Purchases: Practices conference at Skolkovo, the bauma trade fair in Munich, and Quorum’s 15th Corporate Supply Management Conference for Procurement Directors).
As part of arranging and streamlining our work on returning materials and equipment after use (dismantling), the Procurement Department works within its remit to determine the list of the equipment and materials to be returned and involve the suppliers in the programme of returning them, including ferrous, non-ferrous, and precious metals scrap and waste, for reuse in our production process.
The involvement of suppliers in the Trade-in programme helps us cut and optimise our business costs.
Procurement management
The Company’s procurement process is certified for compliance with ISO 9001 and ISO 14001.
Our procurement activities are based on formalised procedures and policies, Business Ethics Code of MMC Norilsk Nickel, the Company’s Anti-Corruption Policy, Regulation on the Product Procurement Procedure, and other by-laws of the Company.
In our purchasing activities, we exercise a unified approach to both centralised procurement and procurement organised independently by the Head Office, branches, and Group enterprises. Depending on the expected purchase price, procurement can be organised either as a bidding procedure (tender), simple procurement, or simplified procurement. Procurement procedures may involve collective procurement bodies, such as the tender committee, tender commissions of the Head Office, procurement and tender commissions of the branches and Group companies. In 2019, the Company signed over 3,000 contracts for centralised procurement of materials and equipment worth around RUB 51.2 bn*.
Procurement management
We have adopted category procurement policies. These documents outline common mandatory principles and approaches for purchasing items of a certain category and aim to mitigate operational and financial risks and costs, reduce working capital, make supplies more reliable, and improve the delivery cycle. As at the end of 2019, a total of 37 category procurement policies were in place, including three adopted in the same year. In 2019, the Company purchased ca. 53% of supplies for core operations based on category procurement policies.
In the reporting year, the tender committee and tender commissions of the Head Office in charge of material and equipment purchases, full-cycle projects and IT products carried out procurement for over RUB 32.7 bn*. The Company’s tender committee focuses on improving procedures for identifying reliable suppliers of quality products at a fair market price.
Stronger competition and procurement automation
To handle both centralised (through MMC Norilsk Nickel) and decentralised (at the Group’s Russian business units) procurement activities, we use SAP SRM, an automated system for supplier relationship management. Seven companies from Nornickel Group were connected to this system in 2019.
Creating effective feedback mechanisms, which are also SRM-based, is one of the Company’s priorities for supplier relationship development. To stay informed about and take part in Nornickel’s procurement procedures, suppliers can access Nornickel’s SRM system and talk to experts about any type of product to be purchased. Sign-up for the system is free, imposing no additional obligations and no need to use a digital signature on the users. As at the end of 2019, over 3,200 potential suppliers were registered and licensed to work in the system.
Apart from that, the Company leverages independent bidding platforms, such as Fabrikant.ru and B2B-Centre. These solutions help improve the transparency of supplier selection and enhance the competitive environment as part of the procurement procedures.
In 2019, the Sales, Procurement, and Innovation Unit held a conference to discuss procurement efficiency, new opportunities driven by SAP ERP, environmental and NID development projects, as well as progress towards performance improvement and lean production.
Supplier selection
Nornickel has in place a multi-level supplier assessment system that complies with ISO 9001:2015 Quality Management System.
The Company applies a life cycle costing approach to selecting suppliers, which includes the costs of ownership and subsequent utilisation, and follows formalised procedures which are based on the following principles:
- equal competitive opportunities for suppliers;
- comparison of business proposals from qualified suppliers according to pre-approved, objective and measurable criteria;
- division of procurement functions and responsibilities by roles;
- a multi-step process of procurement decision-making.
- the results of the qualification-based selection and suppliers of the costliest items are approved by the collective procurement body comprising representatives from various functions of the Company.
Compliance with the above supplier selection criteria makes the decision-making process transparent and maximises the Company’s benefits by helping to reasonably choose the best available offer.
Nornickel pays close attention to developing relations with manufacturers of equipment and materials, as they ensure the Company’s ability to meet its strategic targets. We are committed to working with more local suppliers. To this end, we developed a centralised pilot testing procedure enabling us to promote competition and phase out imported equipment with that manufactured locally. Foreign suppliers are mainly engaged for delivering unique equipment or systems that do not have Russian alternatives. In 2019, the Company completed 24 pilot tests, 16 of which were deemed successful (including 12 pilot tests of Russian-made materials and equipment). As at the end of 2019, 22 pilot tests were in progress. The Company established cross-functional commissions to identify promising areas for scheduled pilot tests aimed at achieving import substitution.
In 2019, the Company’s Procurement Department and the Investment and Industry Department under the Yaroslavl Region government signed a production cooperation memorandum to implement locally developed hi-tech solutions at Nornickel sites. The meeting minutes envisage:
- measures to compile a list of relevant products and their application areas/projects;
- assessment of local goods’ compliance with specifications and import substitution requirements of the Norilsk Nickel Group companies;
- competitive selection of vendors and suppliers;
- pre-qualification of vendors and suppliers.
All our procurement activities rely on the regulated procedures and policies and are in full compliance with federal laws on procurement of goods, works and services by certain types of legal entities.
Supplier feedback channels
To maintain an ongoing dialogue with suppliers, our website has a dedicated Suppliers page, which provides key information on the Group’s procurement principles and procedures and planned material requirements. The page also features announcements and invitations to participate in the Company’s tenders.
Our procurement experts make up an active part of the professional community in relation to the respective procurement areas, attending industry exhibitions and participating in conferences organised by professional communities.
Creating effective feedback mechanisms is one of our priorities in developing supplier relations. We have put in place SAP SRM, an automated solution for supplier relationship management. This gives the suppliers continuous access to information relating to the Company’s procurement procedures. Over 3,200 potential suppliers are currently registered and licensed to work in the system.
Integration of responsible management and sustainable development principles into the supply chain
In our relationships with suppliers, we aim to create shared information environment and values. An ESG clause is incorporated into the standard agreement with suppliers and contractors. We adhere to a number of codes of conduct applied by our business partners and devised by foreign manufacturers.
Nornickel evaluates the business reputation, reliability and solvency of potential counterparties to mitigate risks.
Requirements planning and supply management
Material requirements are determined based on production plans and the needs of other business lines. At the planning stage, the Company defines health, safety and environment, as well as other mandatory and optional product and supplier requirements, including availability of certificates, permits, and licences. The resulting data are used to create a material and technical procurement plan.
Accurate planning and availability of stock are key to uninterrupted operations at Nornickel Group. At the same time, we pursue inventory optimisation to minimise our working capital.
Nornickel’s procedure for requirements planning and inventory management is governed by the internal regulation on Procurement Plan Development, Review and Approval, as well as the Implementation Standard of Inventory Management System for Materials and Supplies at MMC Norilsk Nickel.
In 2019, Nornickel executives achieved further progress in improving inventory management and streamlining planning and procurement processes. Following the full-scale roll-out of optimisation across the Company’s major assets, the reporting year saw a significant decrease in surplus inventories (by 9%, or RUB 1.5 bn) for core and investment operations. Total inventories (excluding materials in transit) in the same perimeter went down 7% or RUB 4.5 bn. Our management focuses on preventing the accumulation of slow-turnover inventories by further streamlining business processes.
Control of non-financial factors in supplier relations 103-2
Procurement stage |
By-laws and other control tools |
Control of non-financial factors |
Procurement initiation |
Scope of supply/work: legal and regulatory requirements of the Company, mandatory and recommended specifications of products and services, covering health, safety and environment, etc. |
• • • • |
Procurement documents: provisions for no signs of bankruptcy, overdue taxes and charges, and no criminal records in the biographies of top managers |
• • • • | |
Procurement policies for certain product categories may specify quality assurance procedures for supplies |
• | |
|
||
Procurement procedure |
Qualification of suppliers: default risk assessment and compliance with the Company’s initial requirements (scope of supply/work, specifications, etc.) |
• • • • |
Corporate Security’s checks into business reputation, reliability, and solvency of potential counterparties |
• |
|
Analysis and evaluation of bids submitted, including track record of similar projects and qualifications of key employees |
• |
|
|
||
Contracting procedure |
Inclusion of an anti-corruption clause in the contract |
• |
Inclusion of product and service specifications in the scope of supply/work |
• • • • |
|
|
||
Contract performance by suppliers |
Corporate Procedure for Organising and Conducting High-Hazard Operations: control over contractors’ compliance with health and safety requirements |
• |
Control over compliance with the Company’s initial requirements (scope of supply/work, specifications, etc.) and environmental regulations during work and upon acceptance |
• • • |
Key non-financial factors:
• |
Quality of products, works and services |
• |
Environmental protection |
• |
Occupational health and safety |
• |
Legal compliance |
Product quality and supply reliability
We at Nornickel Group have achieved utmost efficiency in our production operations to provide the volumes, quality, and product range*that meet the needs of society while also fully complying with all applicable laws and HSE requirements.
In 2019, the management systems of MMC Norilsk Nickel and Gipronickel Institute successfully passed surveillance audits, while the systems of Kola MMC were subjected to a recertification audit. At Norilsk Nickel Harjavalta, inspection audits focused on ISO 9001 and ISO 14001 compliant management systems, and an ISO 45001 certification audit was carried out on its occupational health and safety management system. A total of 130 employees underwent training in quality management, including 13 in the Head Office, 43 at Polar Division, 28 at Kola MMC, two at NORMETIMPEX and 44 at Norilsk Nickel Harjavalta.
We have put in place the Corporate Integrated Quality and Environmental Management System.
Polar Division’s M00k copper cathodes (GOST 859-2014 and GOST 546-2001) are certified in the GOST R certification system for compliance with the applicable product regulations and are registered on the London Metal Exchange (LME) under the NORILSK brand.
Kola MMC’s nickel cathode brands of SEVERONICKEL COMBINE H-1Y and SEVERONICKEL COMBINE H-1 are registered on the London Metal Exchange and Shanghai Futures Exchange.
In 2018, nickel cathodes were registered on the LME under the NORNICKEL brand, with the NORILSK I electrolytic cobalt following suit in 2019. With a purity rate in excess of 99.8%, Kola MMC’s premium electrolytic cobalt grades are unrivalled in Russia. Globally, only a handful of companies can match this level.
Corporate Integrated Management System (CIMS)
Products offered by Norilsk Nickel Harjavalta Oy, in particular, nickel brands of NORILSK NICKEL HARJAVALTA CATHODES and NORILSK NICKEL HARJAVALTA BRIQUETTES, are also registered on the LME.
The Company’s goods are labelled to keep the customers and carriers informed about key properties of the products (including those meant for exports). The labelling rules are set out in product-specific regulations and take into account the GOST 4192-96 (Labelling) requirements and contractual obligations.
In 2019, the Company faced no major fines for a failure to comply with product supply rules and requirements.
Sales policy
In sales, we seek to build long-term strategic relationships with key market players. When it comes to nickel products, our sales strategy focuses on achieving a balance between supplies to stainless steel manufacturers and to other industry stakeholders. 102-4 102-6
As the world’s largest producer of palladium, we continue to implement the strategy of entering into direct long-term contracts with end customers to ensure sustainable and strong demand for platinum group metals. For details on our sales policy, please see the 2019 Annual Report.
In 2019, our customer base exceeded 400 entities (mostly industrial companies). Nornickel sells its products in all key markets, with its footprint spanning 37 countries as at the end of 2019.
Customer satisfaction monitoring
Buyers of the Company’s key products are surveyed to assess their satisfaction on an annual basis, while those purchasing sulphuric acid are asked to complete relevant questionnaires once every three years. Compliance with contractual obligations is audited and analysed on an ongoing basis. Survey results provide insights into the effectiveness of customer satisfaction initiatives over the past year and help identify more areas for improvement.
The key to positive survey results is maintaining or exceeding target customer satisfaction level at 2.50 points (out of 3 points). Surveys must cover key customers accounting for at least 50% of total product sales. According to the 2019 survey, the customer satisfaction level stood at 2.70 points.
In 2019, we received 39 complaints and grievances about product or service quality and achieved out of court settlement for all of them by meeting the demands of customers (23 complaints were deemed unfounded). As at the end of 2019, two grievances were still being processed, with remedial action plans developed to address 17 complaints (including six that had been rejected).
Markets and production volumes*
Market environment |
Price trend |
Company’s production volume |
|
Nickel market |
reduction of shortages |
growth |
228.7 kt |
Palladium market |
reduction of shortages |
strong growth |
2,922 koz |
Platinum market |
growth of oversupply |
moderate decline |
702 koz |
Сopper market |
reduction of shortages |
decline |
499.1 kt |
Revenue from key metal salesin 2019 by region, % 102-6
Innovations
R&D and innovation play a major role in taking forward Nornickel’s strategic priorities, from expanding our production to improving efficiency and reducing environmental impact.
For the most part, these key areas of development are handled by the Company’s two dedicated business divisions — Gipronickel Institute (part of the Group) and Nornickel Digital Lab.
On top of that, we have an R&D Panel in place set up back in 2013 to improve the quality of decision-making in the R&D process.
Gipronickel Institute is one of Russia’s largest research and engineering centres for mining, metallurgy, concentration and processing of minerals that is in charge of Nornickel’s R&D and feasibility studies. The institute is engaged in developing standard operating procedures (SOPs) as well as upgrading and supporting all key operations, including ore mining, concentration, pyrometallurgy and hydrometallurgy.
Among the highlights of 2019, the United Nations Economic and Social Council (ECOSOC) approved a resolution “Combating transnational organised crime and its links to illicit trafficking in precious metals” that leveraged Nornickel’s singular technology to identify PGM-bearing items, which testifies to the strength of our R&D team.
Nornickel Digital Lab was established in 2018 to focus on research based on digital technologies. The lab tracks new technologies and emerging business models, collects, collates and analyses digital initiatives, and prototypes new solutions that will help streamline our processes and eliminate production bottlenecks and inefficiencies. The lab team includes engineers with extensive hands-on experience, highly qualified mathematicians and IT specialists.
In two years since inception, Nornickel Digital Lab accumulated over 130 concepts, with over 30 initiatives being under active development and 16 completed and pending potential implementation.
Among the lab’s key 2019 projects was collaboration with the South-West State University to develop industrial exoskeletons for the mining industry*.
Made of light and durable aviation aluminium, Nornickel’s industrial exoskeletons reflect biomechanics of human movement. They transfer the load from the human’s spine to their own metal framework. Workers put on exoskeletons over their workwear and adjust them with belts. Our initial tests showed that one worker wearing an exoskeleton is as productive as three workers exposed to heavy manual labour. Exoskeletons are most useful in operations with heavy hand tools, laying pipes, loading and unloading, and installing metal structures. According to preliminary estimates, the use of such exoskeletons may greatly improve both employee productivity and safety.
The basic exoskeleton design may feature an integrated Global Navigation Satellite System (GLONASS), a sensor for load measurements, and additional lights.
In 2019, we displayed our industrial exoskeletons at an advanced technology exhibition visited by Russia’s President Vladimir Putin and organised by the Agency for Strategic Initiatives (ASI) as part of the National Technology Initiative for Russia’s leadership in global technology markets by 2035.
As at the end of 2019, pilot tests of exoskeletons were run at Norilsk Mining and Metallurgical Plant, Talnakh Concentrator and other Company facilities. Some partner industrial companies also had an opportunity to conduct on-site tests of our exoskeletons and provide their feedback.
In 2020, Nornickel plans to continue commercial testing of industrial exoskeletons with a potential to subsequently expand their production based on the testing results and demand for this solution.
Digital technology
The development of digital technology is one of the most significant trends shaping today’s economy. Digital solutions have the potential to significantly impact the global division of labour and become a key factor in increasing labour productivity in the medium term.
Nornickel leads the charge among Russian industrial producers in bringing digital technology to production and takes an active part in building the national legal and regulatory framework in this area, which is also one of the key aspects of the Digital Economy national project. Vladimir Potanin, President of MMC Norilsk Nickel since 2018, has chaired the working group of the Russian Union of Industrialists and Entrepreneurs for coordination of legislative and regulatory efforts in the realm of digital economy.
The key elements of Nornickel’s digital transformation:
- introduction of automated management systems;
- digitalisation of mining management processes;
- development of business solutions based on the distributed ledger (blockchain) technology;
- other projects in industrial robotics, the Internet of Things (IoT), big data analysis, digital twins and other innovations.
In 2019, we signed a number of cooperation memoranda with Russian and foreign companies from various industries and focused on collaboration with major market players to share experience in leveraging artificial intelligence, machine learning, blockchain and other advanced technology to eliminate bottlenecks and improve safety at our industrial facilities.
The opportunities of the sharing economy tested by us in the course of such cooperation will enable industrial companies to monetise their know-how, while also helping them significantly accelerate innovative development and manage their internal R&D processes effectively.
Digital innovation in mining management
Technology Breakthrough is an ongoing programme to introduce advanced digital technology in mine engineering, as well as in planning and operational control of mining activities.
The Digital Mine project is one of the key initiatives of the programme, which seeks to boost operating efficiency of underground mining by:
- centralising planning and control of mining operations based on real-time data analysis;
- developing an automated system for shift-to-shift planning of mining operations over a ten-day horizon.
The project will bring a number of positive benefits for Nornickel, enabling the Company to enhance safety of underground operations and provide training opportunities for employees (simulation-based training, management skills training), and also supporting the creation of new jobs (such as a remote control operator of self-propelled drilling rigs / load-haul dumpers, etc.) in the long term.
We already monitor around 80% of our production processes in real time. All of our mines can effectively track their current production indicators at cycle-level granularity.
We are now considering possible roll-out of 5G or LTE networks to support our dynamic production environment. This will bring connectivity to the most remote parts of the mine and enable real-time data transmission by all underground equipment.
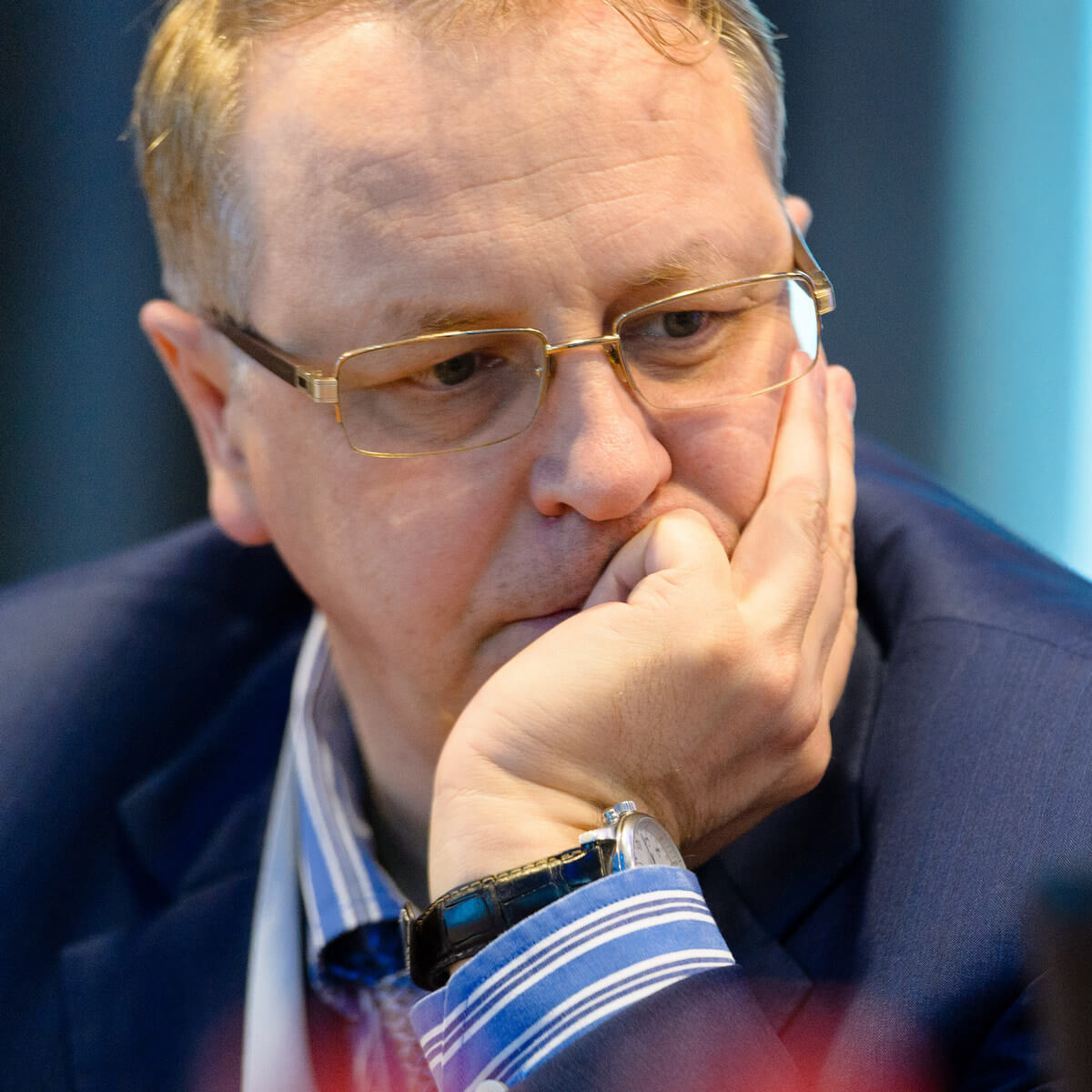
Sergey Dyachenko
First Vice President
and COO at MMC Norilsk Nickel:
Early in the project, communications and tracking infrastructure was set up for locating people and equipment underground, including a fiber-optic network and a wireless data transmission system, with tags worn by all mine personnel or installed in all mining equipment to track their movement.
As at the end of 2019, state-of-the-art operational control centres supporting 24/7 real-time mining operations monitoring were launched at five mines of Polar Division (Oktyabrsky, Taimyrsky, Komsomolsky, Skalisty and Mayak). In 2020, Nornickel plans to launch similar centres at Kola MMC’s Severny Mine.
Nornickel is also working on the Automated Mining Management System project to enable real-time performance monitoring of shift assignments, with data transmission devices installed on load-haul-dump vehicles, self-propelled drilling rigs and underground electric locomotives.
The system greatly accelerates data exchange, which, in turn, can help increase the volume of ore mined, cut costs, and boost efficiency of human resource management.
Launched at Kola MMC’s Severny Mine in late 2019, the Automated Mining Management System is planned to be rolled out at Polar Division’s Oktyabrsky, Skalisty and Komsomolsky mines in 2020.
On top of that, many mines are now testing electronic job orders. As part of this exercise, electronic logs, which are being gradually introduced in our operations, are filled out online by our mine experts based on visual inspection and assessment of each section’s condition to record any ongoing changes. At the end of shift, these logs can be used to generate job assignments for mechanics, power engineers and other employees.
Nornickel is also developing:
- independent drones capable of taking video deep inside a mine without GPS guidance. These devices contribute to occupational safety;
- a robotic system equipped for laser scanning and capable of autonomous navigation in the mine. The robot can do high-quality 3D mine surveying, including hard-to-reach areas, and the results can be integrated into the MGIS.
Automated management systems
Nornickel is actively introducing automated management systems at its enterprises to streamline procurement, financial and HR processes.
In addition to covering the Company’s Head Office, Kola MMC and Bystrinsky GOK, in 2019 the SAP ERP system was also launched at Polar Division.
In addition, we have developed an ERP roll-out roadmap that defines the list of enterprises to join the centralised system over the next several years and schedules respective timelines. In 2020, an SAP ERP system is planned to be launched at transport divisions and other sites of MMC Norilsk Nickel.
In 2019, Nornickel completed the roll-out of an ERP system across its operations in the Norilsk Industrial District, which became one of its most ambitious business automation projects. The project was successfully completed in just 18 months despite the impressive scale of coverage, geographical remoteness of production assets, and severe climatic conditions of the Far North. It won the gold award in the Business Transformation category at SAP Quality Awards — 2019, and we are extremely proud to see it recognised by the expert community.

Sergey Malyshev
Senior Vice President
and CFO at MMC Norilsk Nickel:
In early 2019, Nornickel launched a project to automate insurance premium adjustments reporting based on a new HCM solution — the Report Management System (RMS). The decision to develop this system came in response to Order of the Federal Tax Service of Russia No. ММВ-7-11 / 551 dated 10 October 2016 that required the Company to report adjustments to prior-year statements to the Federal Tax Service.
Its launch opens up opportunities for businesses to produce reporting without manual adjustments and reduces the time for their preparation. Today, the RMS solution is used across three of Nornickel’s enterprises, whose aggregate headcount exceeds 12,000 employees.
Commercialising innovation in collaboration with SAP
In 2019, Nornickel Digital Lab began cooperation with SAP with a view to commercialising Nornickel’s innovations. In the same year, the lab released two proprietary solutions built on SAP’s open source software and offered them for sale through a special platform of the German manufacturer:
- conveyor contaminant video identification system for concentration facilities;
- thermal imaging short circuit video identification system for copper electrolysis shops.
Both solutions can help significantly increase productivity by preventing production shutdowns associated with the need to fix technical issues.
The lab’s conveyor contaminant identification project won the golden award at the MineDigital Competition held as part of the MINEX Russia 2019 mining forum.
Blockchain
Tokenisation of assets
Thanks to embracing and using distributed ledger systems (blockchain) and the tokenisation technology, Nornickel, as the industry’s digital leader, has gained a number of significant competitive advantages, including security, speed, transparency, higher liquidity of digitised assets, lower costs, provenance and confirmed quality of metal-bearing products, and a potential to attract a new class of investors.
Nornickel is one of the first industrial companies to embark on the concept of selling tokenised products with ambitious goals of offering a wider range of options, managing sales policy in an efficient manner by using modern digital technologies, identifying new markets, and attracting funding on more favourable terms.
The key infrastructure for data implementation will be a tokenisation platform, which is currently developed in partnership with IBM, a global IT leader. Industry majors have been invited to pilot the contract tokenisation feature.
Another promising practical application of blockhain in the industry is ensuring a higher value chain transparency as part of implementing the responsible production and consumption concept.
Engagement with the professional community
In 2019, we joined the Hyperledger Project, a global collaboration hosted by the Linux Foundation, one of the largest and most reputable technology consortia supporting the creation of sustainable open source ecosystems. Hyperledger is an open source collaborative effort created to advance cross-industry blockchain technologies as well as to build a framework for efficient global corporate and research partnerships to promote the most successful solutions.
In October 2019, Nornickel helped host Russia’s first ever Hyperledger Bootcamp, a major educational and networking event for IT professionals and startups, as well as representatives of large companies involved in IT development and support.
The participants had an opportunity to get together in an informal setting to share expertise, get insights into the key open source trends and case studies, and exchange experience in new project and technology development. Among them were executives of the Hyperledger Project’s global team as well as representatives of Norilsk Nickel, Sberbank, Russian Railways, Intel, Oracle, various startups, and major educational institutions offering programmes in technical majors. Nornickel’s specialists participated in a number of sessions as speakers and invited experts.
Digital talent pipeline
In 2019, as part of its efforts to build a talent pipeline, Nornickel signed a trilateral agreement to launch a master’s programme in blockchain at the Moscow Institute of Physics and Technology (MIPT). The agreement was signed at the St Petersburg International Economic Forum between Nornickel, MIPT and IBM, a global leader in digital technology and blockchain. The initiative is designed to provide career incentives to students, while also supporting innovative competence building on a national scale, fostering an environment for the best practices sharing with contribution from industry leaders, and passing on IT experience to subsequent generations.
Nornickel’s strategy seeks to develop its talent pool in cooperation with Russia’s leading technical universities resulting in new competencies with a focus on digital technology. We will prepare today’s students to meet tomorrow’s challenges, so that they can joint Nornickel and help reinforce the Company’s growth and efficiency. In addition to training specialists, a newly set up educational centre will support R&D in technology and the roll-out of promising solutions across Nornickel’s projects.
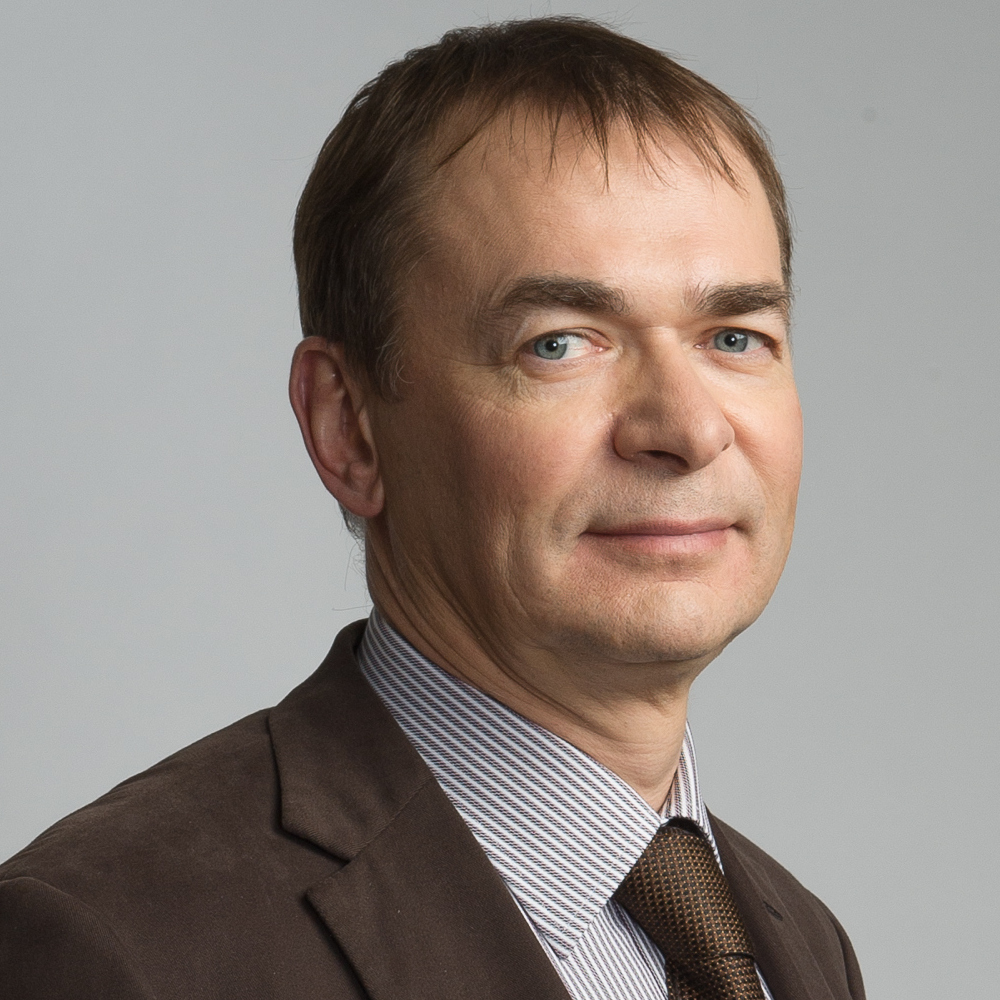
Sergey Batekhin
Senior Vice President —
Sales, Procurement, and Innovation
Transparency
Enhanced transparency and reliable access to information for all stakeholders are the main principles guiding Nornickel Group in its operations.
The Company has in place the following key documents governing transparency:
- Information Policy Regulations
- Procedure for the Interaction between MMC Norilsk Nickel’s Officers and Russian and International Mass Media.
We provide our stakeholders with material information as per the requirements of the Russian law and annually increase the scope of disclosure on all aspects of our operations, which range from production activities to social and economic projects in the regions of operation. We have been keeping up with our commitment to regularly inform the public about our strategy and mission, policies, key events and performance, as well as make clear our position on certain topics.
In the application of our information policy (as approved by the Board of Directors), we are guided by the principles of regularity, timeliness, accessibility, reliability, completeness, balance, and impartiality. Our annual disclosures span production activities, financial performance, and social policy, as well as the environmental situation in areas adjacent to the Company’s facilities, including our mitigation projects and сorrective actions along with their effect on the environment. We seek to constantly improve the quality of information provided in annual reports and reports on sustainable development.
The key channels used to relay information to the stakeholders and the public are the Company’s official website nornickel.com, press conferences, briefings, conference calls, and stakeholder meetings and dialogues. We make sure to explain the Company’s position on events (including emergencies) that call for comments, including through press conferences, briefings, or press releases. To that end, we have put in place an efficient media communications system.
Over the past year, the number of media publications about Nornickel increased by 6% compared to 2018 and exceeded 100,000. In 2019, outlets focused mainly on the production and financial performance of the Company, our updated strategy, relations with local communities, the 2019 Universiade, the Sulphur Programme status, and social and charitable programmes and initiatives.